
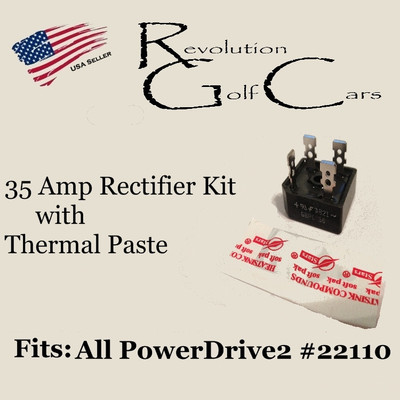
Negative Terminal Connection for the battery pack for charging and connecting the load. The image below shows how we need to connect the cell with BMS. The BMS module has a neat layout with markings for connecting the BMS with different points in the battery pack. The complete explanation of the schematic is done later in the article. The schematic of this BMS is designed using KiCAD. The protection features available in the 4s 40A Battery Management System are: Protection Features of 4S 40A BMS Circuit DiagramĪ BMS is essential for extending the service life of a battery and also for keeping the battery pack safe from any potential hazard. The standard version and enhanced version are almost similar with just a difference of 1 passive component, these variants are not capable of actively balancing the cells, whereas the balanced version has circuitry for balancing the cells. The balanced version has 4 resistors that are capable of load balancing, this feature is not available in the other versions. We will be looking at the Balanced version. This BMS comes in 3 variants, the standard version, the enhanced version, and the balanced version. The image below shows the battery pack which also has a voltmeter, load (bulb), and a female DC jack for the charger, you can read more about it here. We also have another article and video where we have tested the safety parameters of this BMS. I have done complete reverse engineering of this module to find out how it works so that I can show how the BMS works. The practical implementation of the proposed power converter scheme is checked by building a laboratory-prototype to perform an experimental analysis.In this article we will be learning about the features and working of a 4s 40A Battery Management System (BMS), we will look at all the components and the circuitry of the module. Additionally, an efficiency comparison of the suggested converter is carried out with some existing well-known rectifier topologies at different power loads. In order to show the stand-point of the proposed scheme, a fair comparison of the proposed soft-switched converter with an existing soft-switched 3-level neutral-point diode-clamped converter is carried out in terms of the number of components and complexity in the PWM signals generation. The construction, operating principle and simulation analysis of the proposed converter are discussed in detail. The high switching operation with reduced power losses, regulated DC at the output, low-harmonic grid current and power factor correction operation are achieved with the proposed topology. The reduced component stresses and simple control strategy make it an appealing candidate for EV industries to develop this front-end PFC rectifier as a fast battery charger. The proposed topology achieves high efficiency and high power density by employing soft-switching strategy, which is achieved by incorporating a simple auxiliary network in the proposed circuit. In view of this fact, this article proposes a soft-switching three-level T-type vienna rectifier, which can be used as a front-end power stage converter in an on-board EV battery charger. An efficient, compact and fast battery charger is indispensable in order to provide a way to charge an EV in a short time. The proliferation of electric vehicles (EVs) in the transportation market is essentially associated with the performance and reliability of battery chargers. The requirement of high power rated, efficient and high power density grid connected converters has increased due to their extended use in multiple applications such as battery chargers.
